PCBA清洗的重要性
通常电子产品焊接后,其板面总是存在不同程度的助焊剂残留物及其它类型的污染物, 即使使用了低固态含量不含卤素的免清洗助焊剂仍会有或多或少残留物。因此清洗对保证电子产品的可靠性、电气指标、工作寿命有着及其重要的作用 。

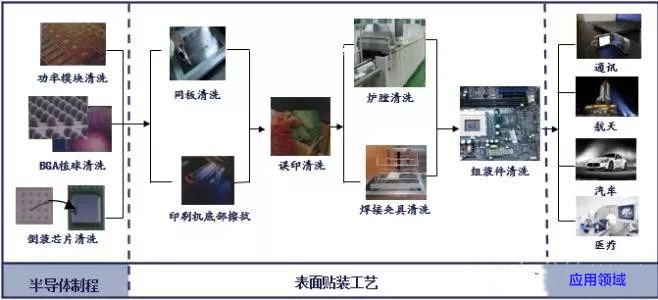


PCBA生产过程中,获得所有潜在污染源的信息是非常重要的。同时我们必须了解清洗设备的清洗能力和确保工艺是否在可控范围之内。指的是有害的残留或者污染物。这些有害的残留物或者说污染物通常可以分成两大类:离子污染和非离子污染,我们先来看看污染物的种类和来源
受到监控的工艺无疑更能够保证产品的洁净度和可靠性对此我们展开了实际的研究。
印制电路组件表面的污染物来源较广,主要包括PCB制作和储运、元器件制作和储运以及组件装联过程中形成的污染。对于印制电路组件而言,所谓污染物,是指元器件或组件的物理、化学或电气性能受到有害影响的表面沉积物和微粒等。一般将组件表面的污染物分为极性或离子污染物、非极性或非离子污染物和微粒状污染物[ 3] ,见表1。
再来看看清洗的方法1 清洗溶剂
根据清洗介质的不同,清洗技术有溶剂清洗、水清洗和半水清洗。水清洗工艺可分为皂化法和净水法。对于采用松香助焊剂的印制板电路组件, 不能采用净水清洗 ,而应采用皂化水清洗;净水清洗工艺主要适用于采用水溶性助焊剂焊接的印制板电路组件。具体各种清洗方法及其优缺点见表2。
2 清洗方法另外考虑到现今电子产品结构设计中出现高密度表面组装工艺,对这些小间距、高密度的表面组装件应有较高的清洁度要求 。手工清洗无法保证板子的清洗质量 ,同时在清洗过程中可能对元器件会造成损伤,特别是对较高的敏感元器件和小间距元器件。现在一般都采用设备清洗。设备清洗的方法可分为:汽相清洗、超声波清洗和水清洗等。而水清洗技术由于适应能力强,清洗质量高,应用最广泛 。
清洗质量的评定标准
根据印制板电路组件用途及要求不同, 对清洗后的清洁度要求也不同, 但其洁净度应符合SJ20896 -2003, 具体见表3。
与印制板电路组件洁净度有关的国外标准 :
(1)MIL-P-28809:该标准中规定氯化钠盐当量离子杂质的最终值必须小于1.56 μg/cm2)。
(2)MIL-STD-2000A:该标准规定离子污染物含量小于1.56 μg/cm2 。
(3)J-STD-601B:该标准规定离子污染物含量小于1.56 μg/cm2 。
另外在标准中还说明了可以用测量电阻率来表示离子污染对印制板电路组件的污染程度:当测试溶液的电阻率大于2 ×106Ω· cm时 ,则表示该组件已清洗干净。
PCBA 离子污染度要求目前对PCBA 有离子污染度要求的相关标准有GJB5807 -2006《军用印制板组装件焊后清洗要求》和HB7262.5 -95《航空产品电装工艺印制板组装件洗》。
航标要求PCBA 清洗后表面离子残留物含量应不大于 3.3 μg(NaCl)/cm2 。国军标要求更加详细,将军用电子产品依据重要程度划分3个等级,并要求:1 级,一般电子产品 ,离子残留物含量应不大于10.0μg(NaCl)/cm2 ;2级, 耐用电子产品, 离子残留物含量应不大于5.0 μg(NaC l)/cm2 ;3 级, 高可靠电子产品,离子残留物含量应不大于1 .56μg(NaCl)/cm2 。
各种材料和工艺使用不同的清洗工艺。而我们通常所说的线路板的清洁度,指的是有害的残留或者污染物。这些有害的残留物或者说污染物通常可以分成两大类:离子污染和非离子污染。
离子污染就是在潮湿空气中的离子形式出现的残留物。残留物来自不同渠道,任何地方都有可能造成离子污染,比如电镀、助焊剂、电离的表面活化剂、乙醇等。离子残留,通常是有极性的,而且有可能在线路板上引起电气化学效应(如果同时还有电子出现) 这些污染物由于不能通过目检发现,其存在尤其危险。非离子污染是指那些在线路板生产之后留下来的不能导电的有机残留物,这些成分通常是高分子、油脂。
在潮湿的环境下,离子污染会通过电子迁移影响印刷线路板的可靠性,进而影响电子产品的稳定性和使用寿命。离子污染导致的两类最常见问题分别是表面腐蚀和结晶生长。
离子污染对印刷线路板造成的伤害
为确保印刷线路板及在清洗工艺之后的清洁度(包括新焊接工艺的导入,新涂层的应用,无铅工艺),对离子污染度的测量必不可少。常用的离子污染度测试方法有离子色谱和离子污染测试仪两种。